Kansai Paint’s Core Technology
- Over the years, our research and development has generated these especially noteworthy technologies shown here.
Based on the three pillars of fundamental technologies—formula design reflecting our expertise in selecting necessary ingredients, powder dispersion to liquefy different forms of powder raw materials, and thin-film deposition to convert liquids into thin films—we have built up an extensive range of underlying technologies through accumulation and combination of diverse technologies.
Each of these is one of Kansai Paint's strengths. We strive to explore and expand our fundamental and underlying technologies further to generate products that continue to deliver ever higher value.
Core Technology
Powder raw materials
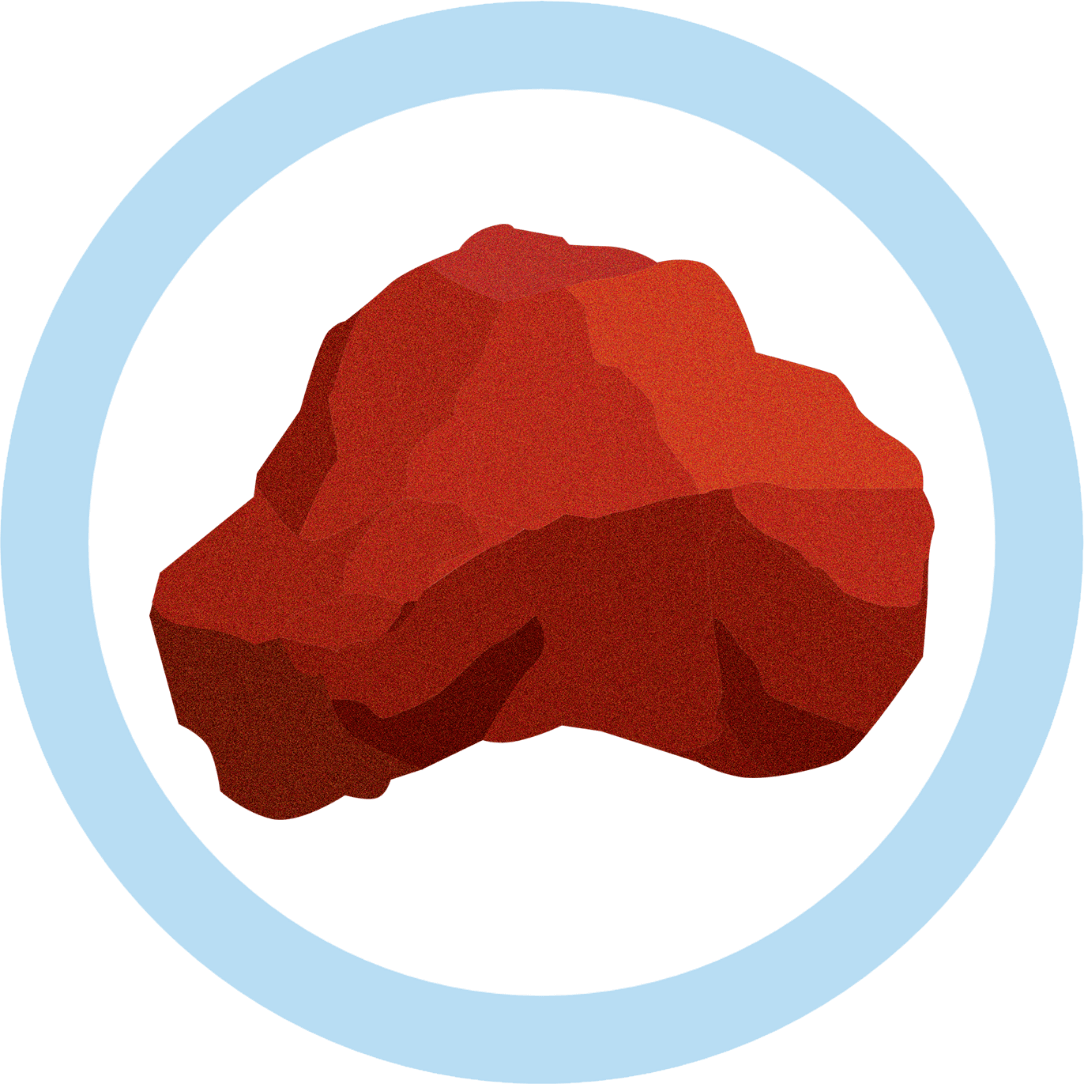
Powder distribution paste
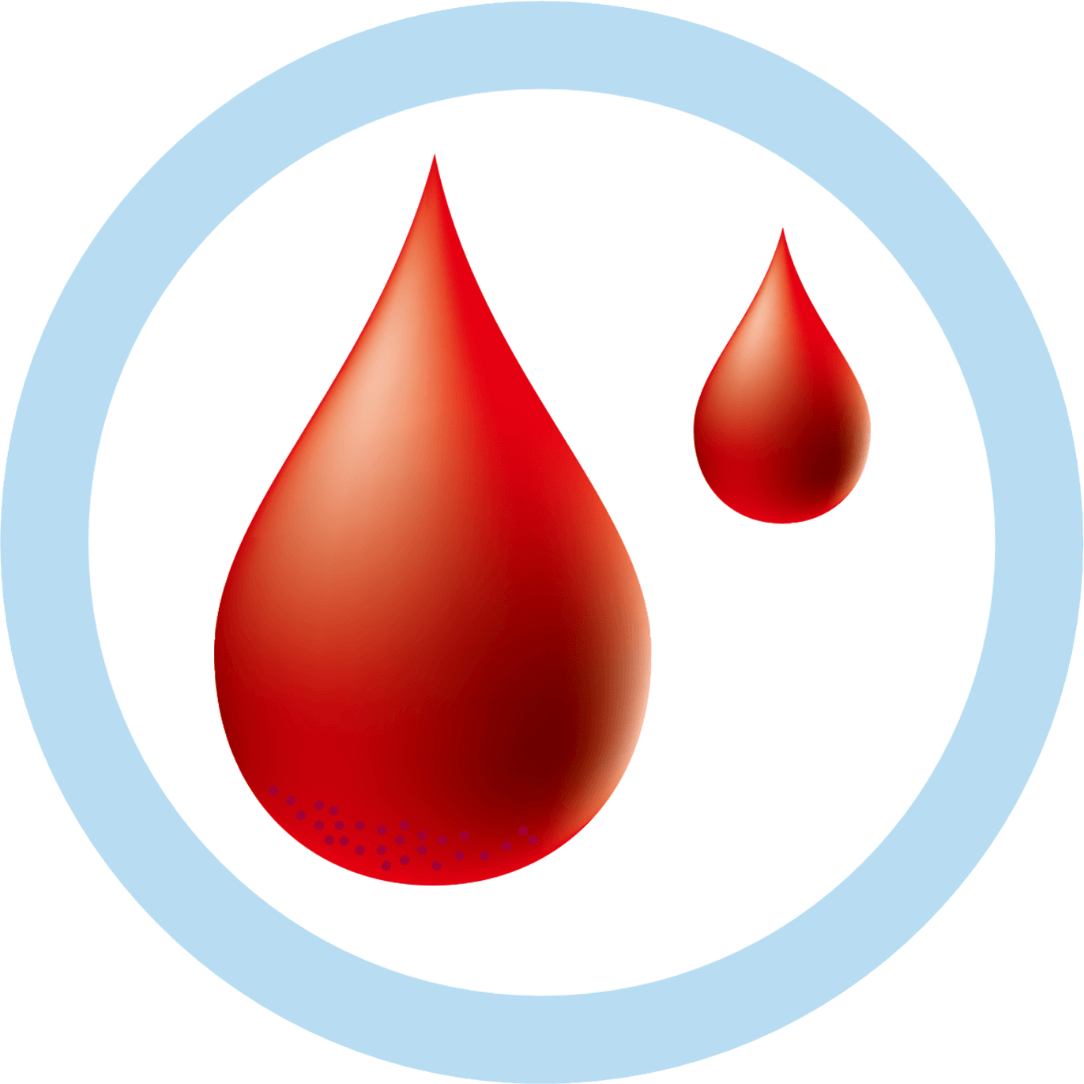
- Particle Dispersion
- This core technology enables dispersion of aggregated particles of optimal dimensions to produce slurry or paste fluids offering the required functions. We combine and optimize underlying technologies such as polymer emulsification and powder mixing.
Liquid paint
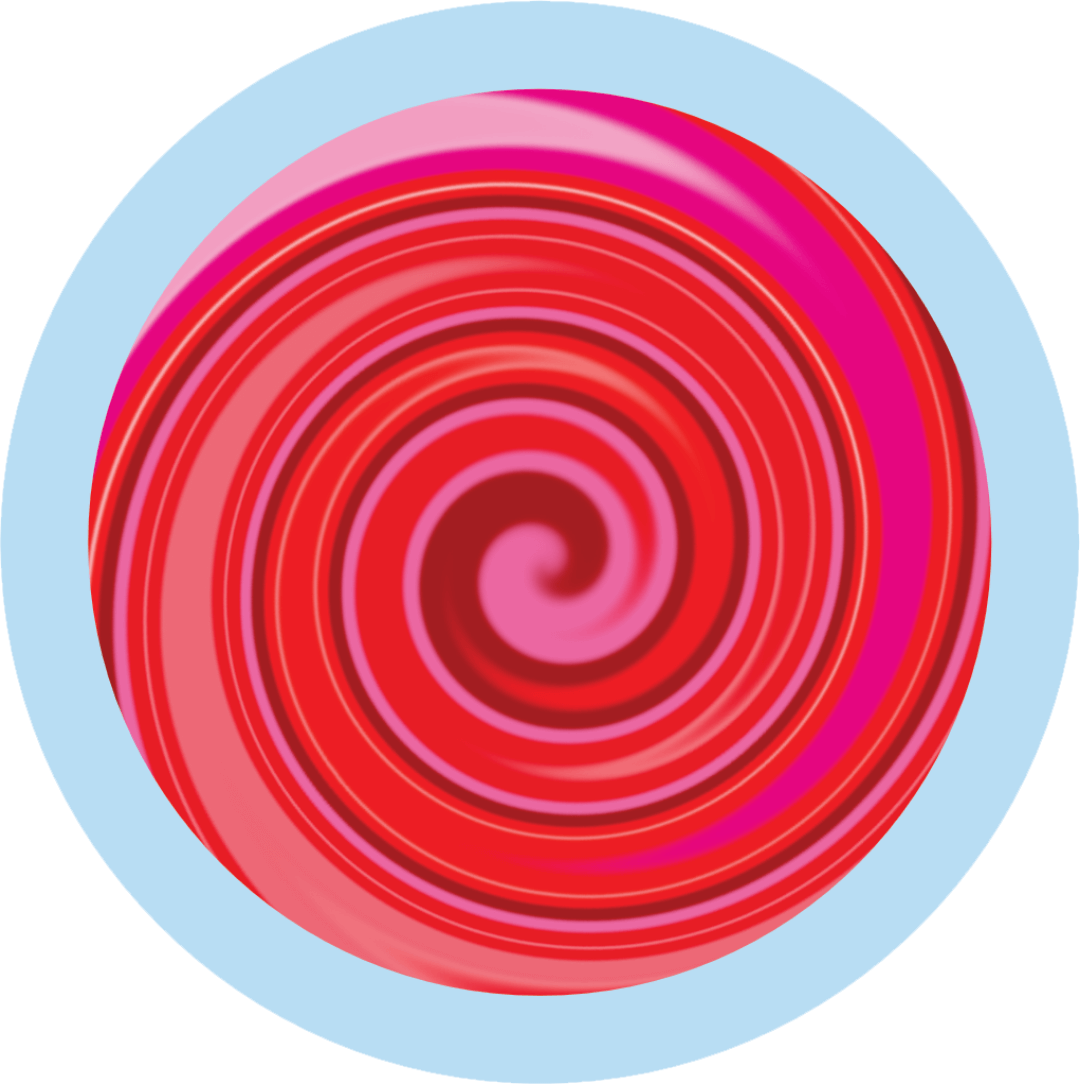
- Formulation
- This core technology provides stable liquids or fluids through dispersion and mixture of multiple ingredients of differing chemical and physical properties. We combine and optimize underlying technologies such as polymer synthesis and selection of coloring materials.
Coat
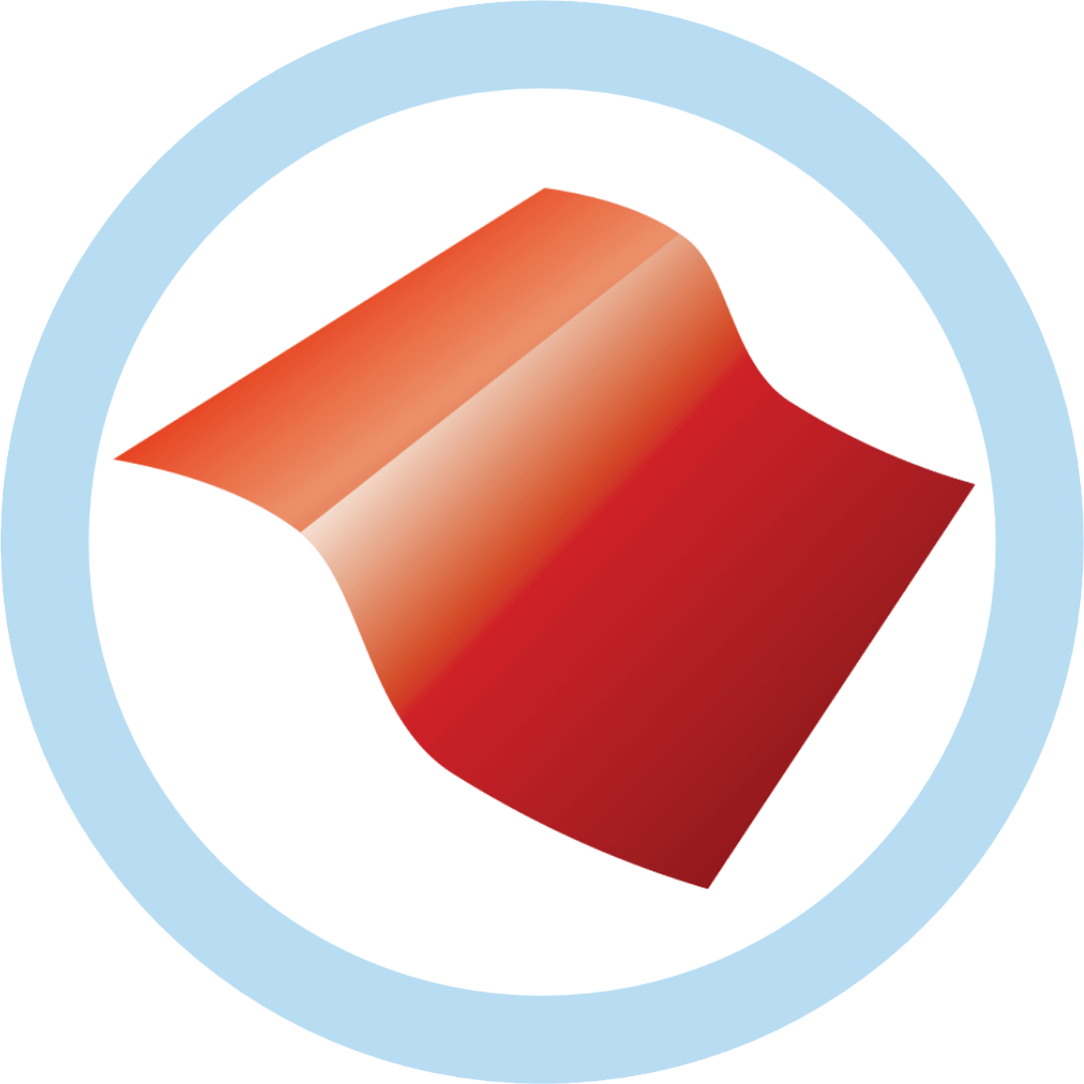
- Thin-film Deposition
- This core technology forms an appropriate thin film on an object's surface to protect and beautify it as well as provide other functions. We combine and optimize underlying technologies, including flow control, coating process design, and multilayer control.
Underlying Technologies
This technology is used to improve object surfaces and to add specific functions to the surface layer, without affecting the characteristics or properties of the object. Depending on customer needs, it provides physical properties such as hardening and hydrophobicity, chemical properties such as biocompatibility and inactivation, or shape properties such as texture and reflectivity.
These technologies form protective layers on object surfaces to prevent rust or corrosion. They maintain the soundness of objects through provision of appropriate properties such as coating cohesion or base-material adhesion and pH cushioning or corrosion-factor barriers, based on identifying the causes of corrosion in the environments of objects.
Photocuring is a method of hardening coatings via exposure to UV or visible light rays. It makes it possible for coatings to harden faster than they otherwise would. We can supply coats for various applications through polymer design, choice of initiators, or optimal irradiation.
We can control the fluidity of coatings by adjusting ingredients and additives, thereby making it possible to supply coatings with outstanding workability that can be stored stably over time. Optimization of fluidity in a semisolid state after application helps achieve dried coats characterized by flawless finish.
Polymer synthesis is used to synthesize polymer resins suited to individual coating applications, using various combinations of monomer raw materials. Control of factors such as monomer types, molecular weight, and straight-chain/branch structure enables customization of optimal polymers from nearly unlimited combinations.
This technology adjusts sub-micron polymer emulsions by introducing oil-soluble polymers into water-based coatings. It ensures stable emulsions through means including proprietary polymer design, choice of optimal emulsifiers and emulsification equipment, and control of transference state.
In partnership with pigment suppliers, we develop organic, inorganic, and metallic pigments useful for color and luster purposes, collecting Big Data on their impacts on coating durability and other performance. Data collection over the years makes it possible to select the optimal coloring materials for specific applications.
Surface treatment and mechanical pulverization are used to achieve even distribution and mixture of powders of differing chemical properties. In addition to supplying powder coatings as powder blends, we also provide stable liquid coatings containing uniform distributions of different powders.
We use ultraviolet-absorbing and infrared-reflecting materials to create coatings that absorb or reflect specific light waves, thereby delivering various coating functions, including thermal insulation or resistance to UV rays. We also harness light scattering, optical coherence, and other properties to control coloring and coating appearance.
This technology can be used to reproduce in digital space the colors and textures of real-world coatings, or to reproduce digital color images in real-world coatings using logic linked to materials already recorded in the system. It's an effective tool for discussions with customers and sharing coating images.
Big Data Analysis
The adoption of computer simulation and statistical analysis approaches has hastened the pace of coating materials development and phenomenal analysis. We identify behaviors at a micro level based on quantum chemistry calculations and seek optimal solutions based on Big Data and AI analysis.
Most coats achieve their comprehensive functions via multiple coating layers. We realize total coats to maximize the performance of each layer, controlling layer mixture and transference with consideration for layer layouts and the coating and drying properties of each layer.
We propose coating equipment and conditions tailored to the desired coating appearance and functions based on our understanding and expertise of coating methods, including spraying and rolling. To achieve optimal coating quality, we control coating surface tension and viscosity in accordance with any restrictions on coating conditions.
We can supply highly durable coatings through choice of polymers and pigments that have optimal chemical ingredients against the impact of light, water, heat, and other environmental conditions. By analyzing wear modes, we reduce the time required for evaluation through testing that simulates long-term exposure.
We increase the repellency and density of coatings to protect them from environmental factors, including water, oxygen, and specific ions that could affect the coated object. We also adjust coating hardness and glass transition points to prevent penetration of sludge, graffiti ink, and chemicals.
To achieve optimal coating adhesion, we reduce the surface energy between the coating and object and introduce polymers and adhesion promoters to anchor coatings. We can also adjust these factors to make coatings easy to peel off.